Project R.A.C.E.
As part of “Project R.A.C.E.” (Reaction Application for Composite Evolution), Hennecke has now made a decisive development step with top industry partners which enables the production of fiber composite hollow parts in a matter of seconds. At the focus of the project is a process chain for production of a motorcycle license plate holder made of carbon fiber composite material with a hollow construction. The traditional license plate holder weighs more than 765 grams, however with the project R.A.C.E., the component exhibits increased performance with a total weight of only 265 grams. That is a weight reduction of over 60 percent!
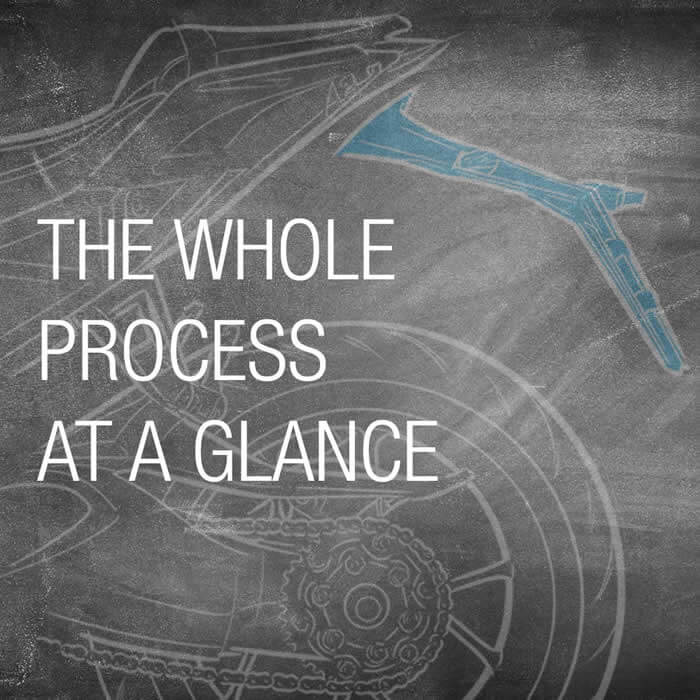
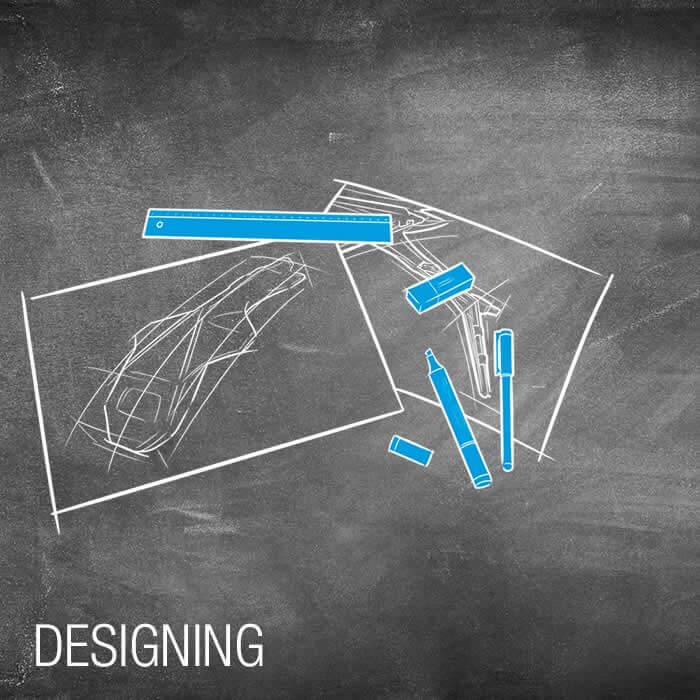
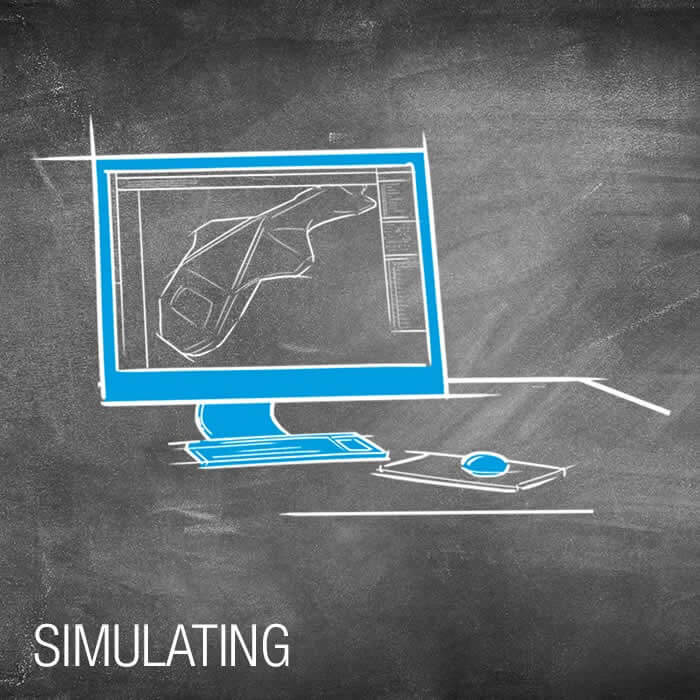
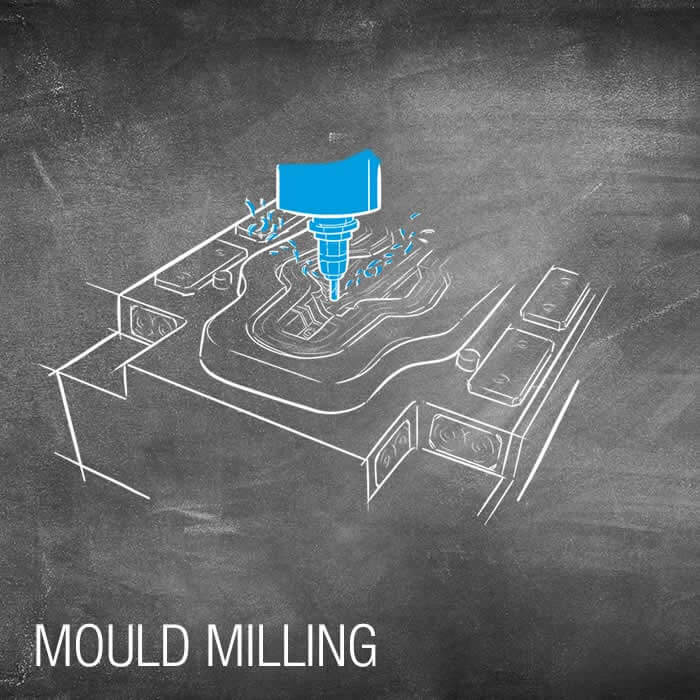
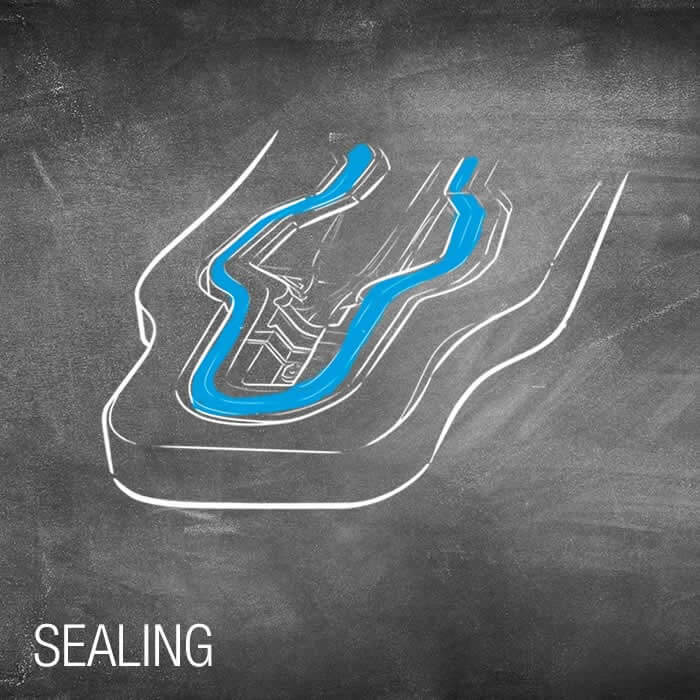
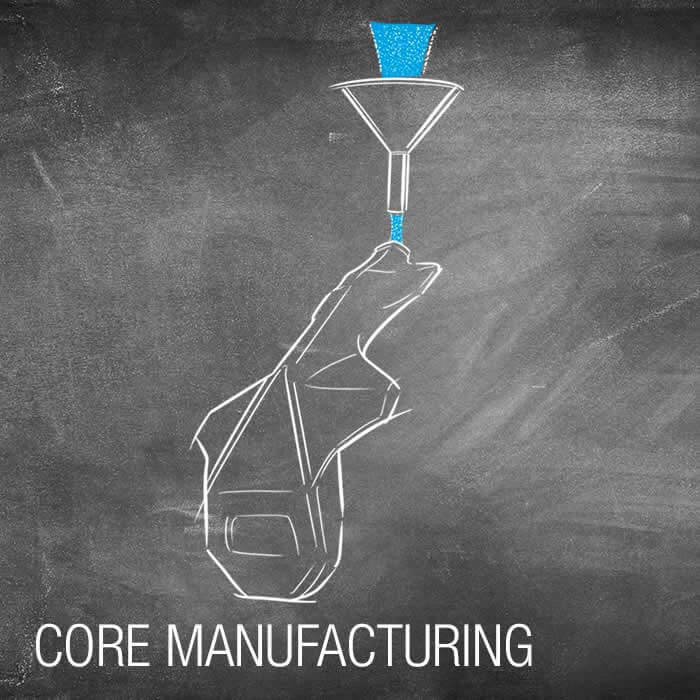
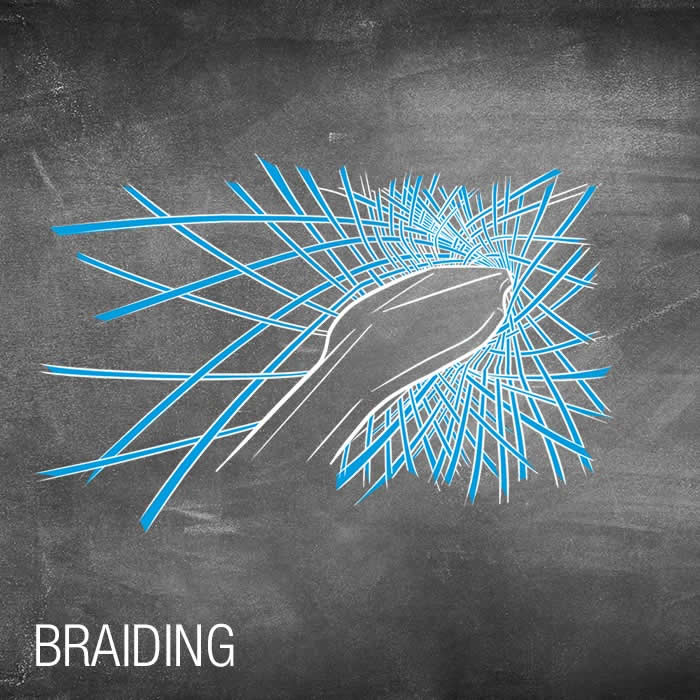
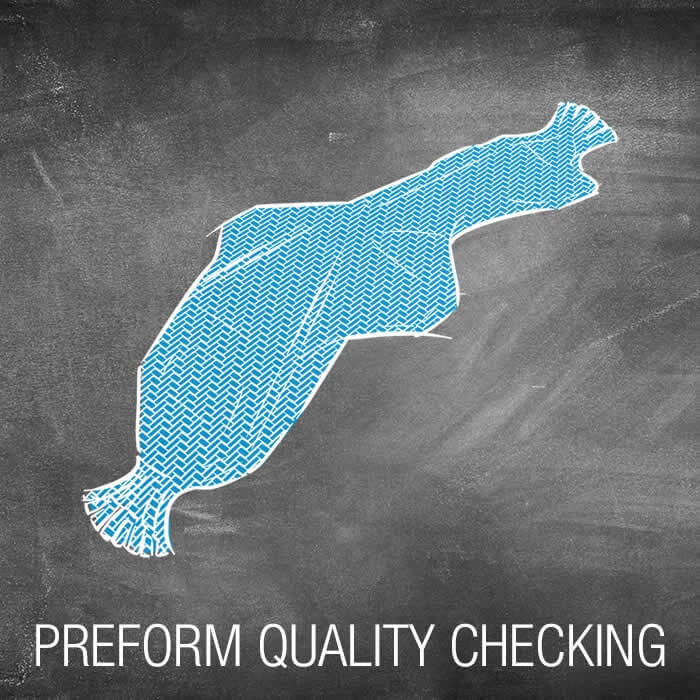
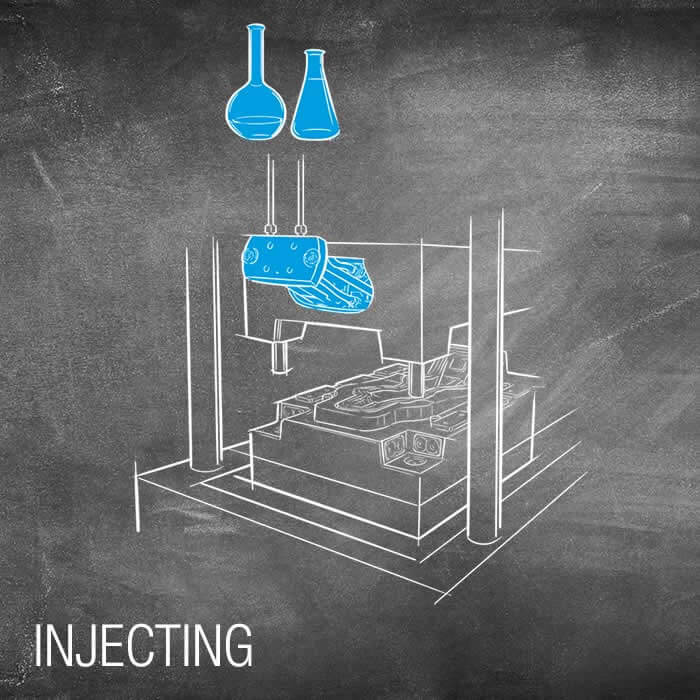
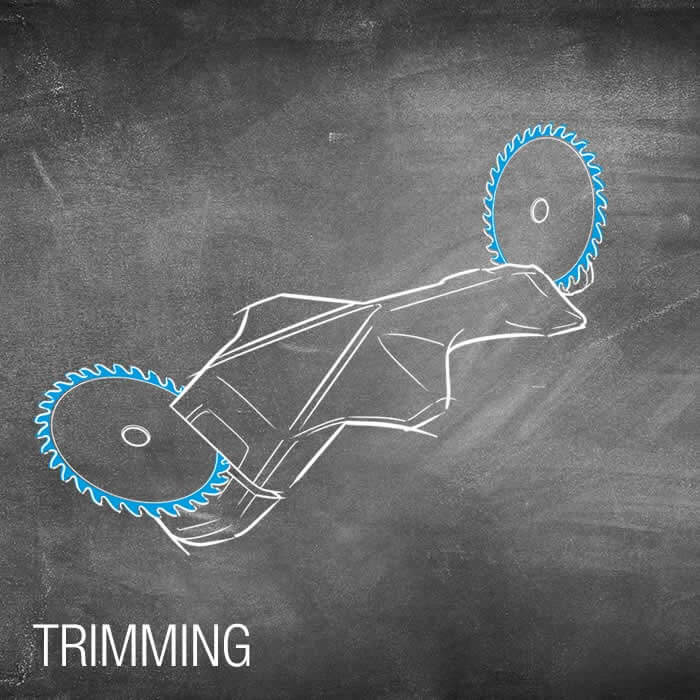
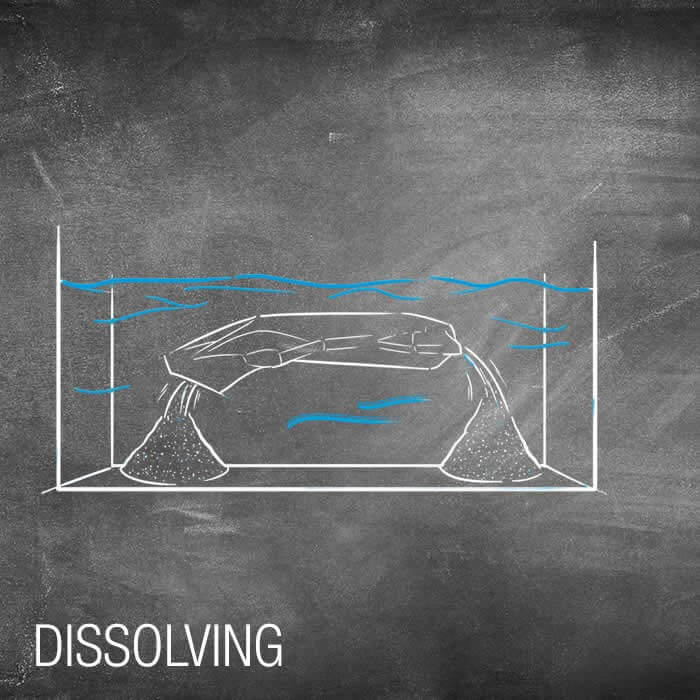
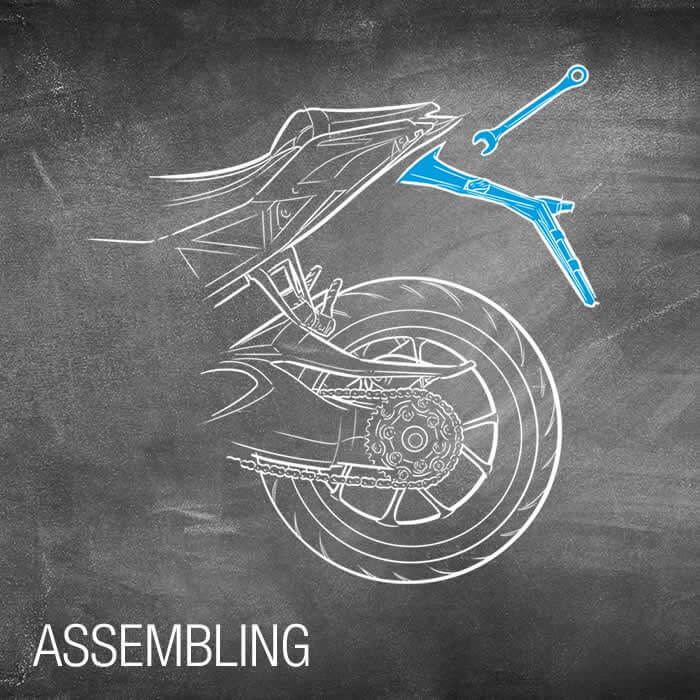
8 partners, 21 specialists, 28 weeks of development time
The framework conditions of the R.A.C.E. project were clearly defined
The interplay of design and engineering forms the basis for a successful component. Kiska-designers and experts of KTM Technologies use the “Inside Out Design” approach for the license plate holder of the Superduke. Initial manual drawings on paper form the basis for the development process that starts simultaneously. Aspects like building space, connection concept and the manufacturability of the component are considered right from the start.
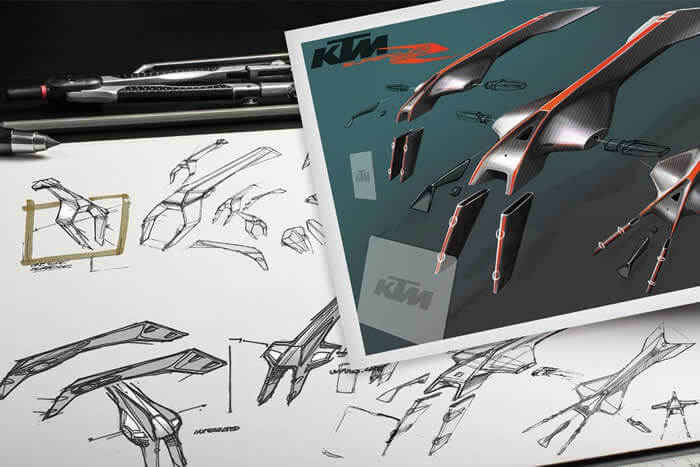
In order to ensure process capability even in the early project phase, the IFB engineers (Institute of Aircraft Design) from the University of Stuttgart use various simulation tools. After the initial sketches are transferred into the CAD software, structure simulations of the component are created, which result in a first estimate of the necessary number of braiding processes. In the next step, these results are used for the braiding simulation, which provides insight about the emerging fiber angles and possible problem zones.
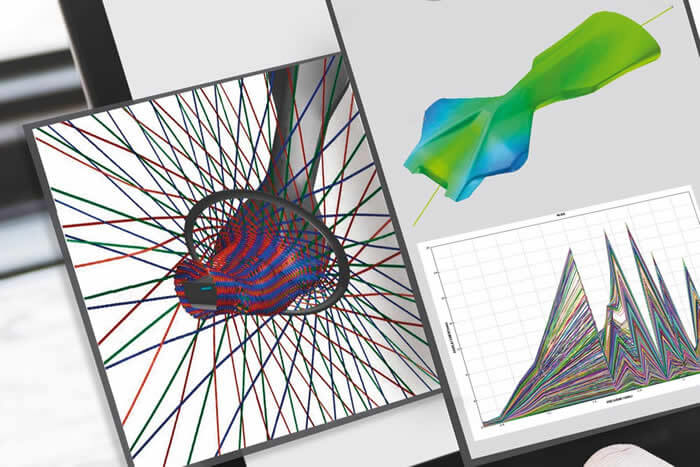
A central element of the CAVUS technology is the sand core of Reinsicht (formerly H2K Minerals). For the R.A.C.E. project, the core was set to a temperature resistance of 330 °C and a pressure resistance of 500 bar. The core also shows its special characteristics after the infiltration of the braid with the matrix. Removing it from the component without increased effort is done with just water. Furthermore, the resulting solution is not toxic. Due to the independent separation of the core components, the elements can easily be separated and recycled. In this process, up to 98 percent of the core is re-usable, depending on the material combination.
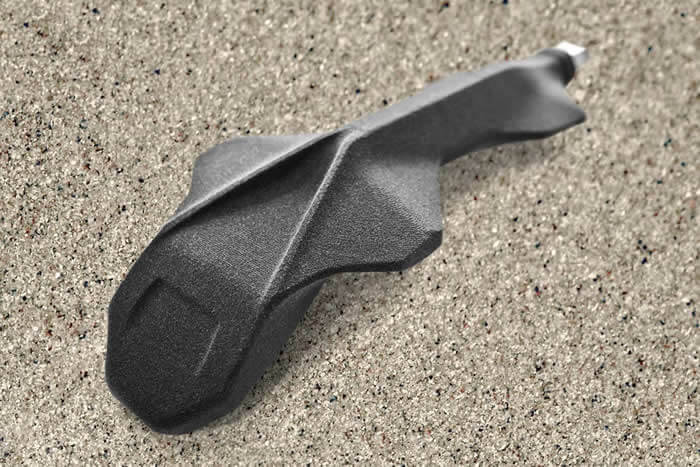
The fibers were applied by the Institute of Aircraft Design at the University of Stuttgart using braiding technology. The core was fixed in a clamping device in the robot of the braiding unit and guided through a braiding wheel following a braid path calculated by the simulation. A Herzog RF 1/64-100 radial braider was used for the R.A.C.E. project. The textile was applied to the core with 64 braid strands consisting of 24k carbon fiber rovings. The strength of the springs in the bobbins determines how tight the braid sits on the core. 600 grams tensile force of the springs provided the best result of flexibility and stiffness for the biaxial braid.
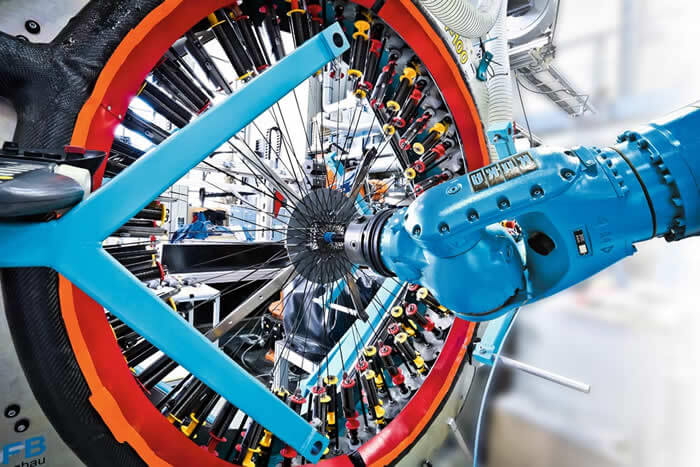
Outstanding mechanical properties as well as excellent processability characterize the polyurethane system VITROX® RTM 332 of the company Huntsman, used for the license plate holder of the Superduke 1290R. The high impact strength and elasticity of the material meet the requirements of the component. Above all things, the processing capabilities are important for the HP-RTM-process, as the cycle time is decisive for series production. With an adjustable “snap-cure” time of less than 30 seconds up to 24 hours, VITROX® enables the shortest cycle times.
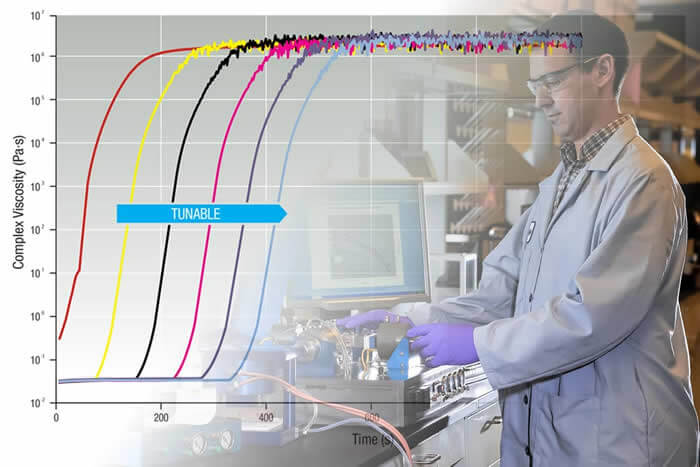
The high and consistent component quality is a particularly decisive argument for using the HP-RTM procedure. In the R.A.C.E. project, the compact system set-up is achieved through a STREAMLINE Hennecke metering machine and an Engel elast 400V vertically closing press. The entire process can be controlled via one system due to the intensive collaboration of Engel and Hennecke. The two components polyol and isocyanate are processed in the STREAMLINE metering plant. A consistent temperature is ensured by the temperature control of the entire system including the tube packet by recirculating the components. Additionally, a homogenized release agent can be injected via a third line.
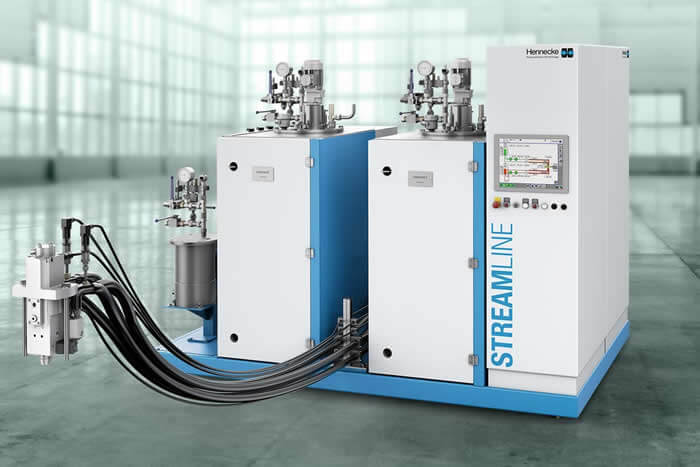
Hennecke uses its newly developed mixhead MN10-3 RTM to mix the components. The high-pressure mixhead can also be used for semi-automatic docking processes due to the conical outlet pipe with integrated internal mold pressure sensor. In order to counteract polymerization shrinkage, the self-cleaning piston also offers the option of applying additional pressure during the curing process of the matrix with hydraulic control. The highest surface qualities can thus be achieved. A further special feature of the MN10-3 RTM is the serial equipment with the patented balanced-pressure injectors. This completely eliminates possible influence of the internal mold pressure on the pressure development of the components.
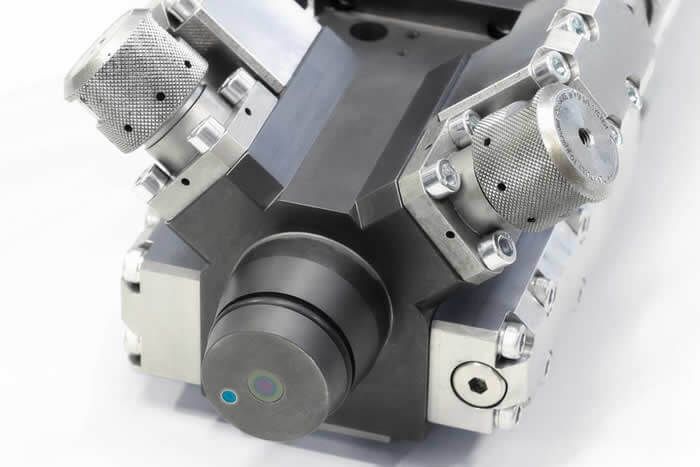
Using highly reactive plastics under internal mold pressures of up to a maximum of 200 bar places high demands on mold technology. On the one hand, the mold must ensure long lifetimes when using the abrasive carbon fibers, and on the other hand guarantee a consistently highly polished surface. Thanks to the expertise of the toolmaker Persico from Nembro, Italy, these requirements were able to be successfully implemented in the R.A.C.E. project. Under average internal mold pressures of around 100 bar, the seal must also meet the highest demands. A novel sealing material of the company Murtfeldt was used for this purpose. Murlock®, a thermoplastic material, provides highest sealing properties for several hundred process cycles. Compared to conventional round cord seals, the material is resistant towards damages by remaining materials or carbon fibers and also chemically inert towards reactive resin systems.
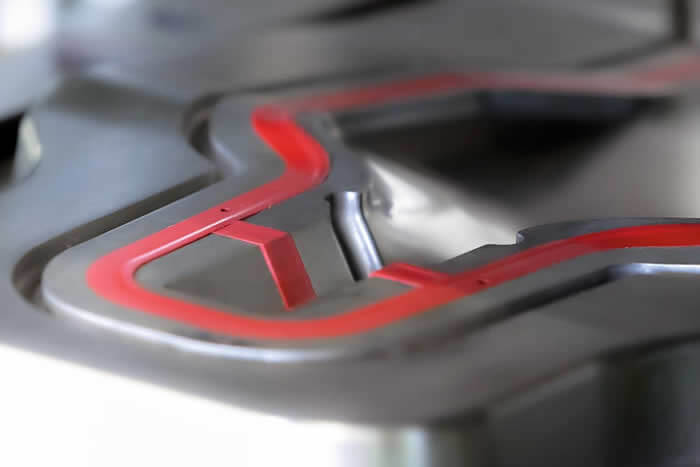
Dissolving the core material with water is a special highlight of the CAVUS technology. The special nature of this process is that the focus is on sustainability. The core can be removed from the component without additional, environmentally harmful solvents. After cutting open the demolded component along the trim lines, it is placed in a water bath. The sand separates in the solution and can be completely re-used for new cores after drying. The binding material in the solution can either be disposed of as process water or can be separated and used as fertilizer in agricultural applications. After the sand is released from the component, it can be added to the conventional post-processing steps of fiber composite components, and finally mounted on the vehicle.
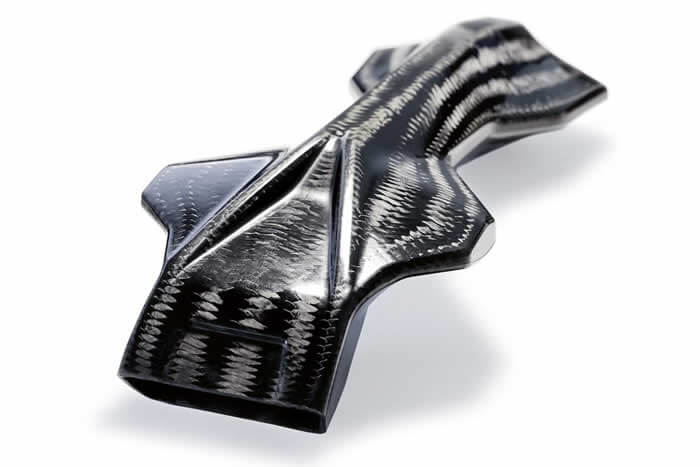
Project partner statements
PROJECT R.A.C.E. “2.0”
License plate holder in hybrid construction (GFRP/CFRP)
The R.A.C.E. project is under constant further development. The latest production approach is a license plate holder in hybrid construction that ensures maximum design freedom in shape and color. The contour in the braiding process is hereby realized with glass fibers. By means of a targeted and therefore load-related strengthening using carbon fibers in the Tailored Fiber Placement process (TFP), the user receives a component that achieves maximum rigidity with minimum weight and significantly reduced raw material costs. In addition, a once again improved core sealing reduces the number of necessary process steps, which additionally minimizes production costs. The new production approach also enables easy integration of electronic components, such as sensor technology or light emitting diodes.